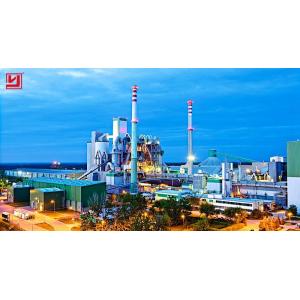
Add to Cart
China supply low investment cement production line cement manufacturing plant
cement plant introduction
(Cement Kiln) is commonly used for the pyroprocessing stage of manufacture of Portland and other types of hydraulic cement, in which calcium carbonate reacts with silica-bearing minerals to form a mixture of calcium silicates. Cement kilns are the core equipment in the cement production process. The capacity usually defines the capacity of the cement plant. As the main energy-consuming and greenhouse-gas–emitting stage of cement manufacture, improvement of cement kiln efficiency has been the central concern of cement manufacturing technology.
Our high-performance dual-wavelength sensors offer unequalled performance for accurate and repeatable measurements on cement kiln applications. These sensors can operate properly when the target energy signal is diluted over 99% by such things as dust and smoke. To effectively measure targets through flames, the 1400 and 4400 Series are recommended. These single-wavelength sensors utilize a very narrow band 3.8 micron filter that provides unequalled performance with measurements through flames.
1. Crushing and Pre-homogenizing:
Most of the raw materials, like limestone, clay, iron ores, and coal, should be crushed before their pre-homogenization. Limestone is the primary material in this line, and due to its large particle size and high hardness, its good crushing plays an important role in the whole line. Special stacking and reclaiming technology has been used in the pre-homogenizing process so that raw materials can be better primarily homogenized.
2. Raw Meal (raw material) Preparing:
Since the raw meal grinding work takes up more than 30% labor force in the whole dry process cement production line, it is quite important to choose appropriate grinding equipment and technological process so that high-quality products can be obtained.
3. Raw Meal Homogenizing:
The raw meal homogenization is a key factor for stable clinker calcination.
4. Preheating and Decomposing:
The preheater is used to preheat as well as decompose raw meal. So the length of the rotary kiln is effectively shortened. And the raw meal can fully exchange heat with the hot gases from the kiln. Because of its rapid and high-efficiency heat transfer, the production efficiency and heat consumption of this production line are greatly improved.
5. Clinker Calcining:
After its preheating and pre-decomposing, the raw meal will be calcined in the rotary kiln, where the generated carbonate will be further decomposed. Meanwhile, a series of solid phase reactions will take place.
Equipment Supply for cement production line
1. Crushing Equipment : Jaw Crusher, Impact Crusher , Hammer Crusher ,Cone Crusher, Compound Crusher ect.
2. Grinding Mill : Ball Mill , Remond Mill , Vertical Mill , Grinding Machines
3. Rotary Kiln / Machnical Vertical Shaft Kiln
4. Preparation Equipments: :Powder Concentrator , Vibrating Feeder, Megnetic Separator ect.
5. Preheater
6. Dyer , Cooler ,
7. Elevator , Belt Conveyor & Bucket Equipments
8. Cement Packing Equipments
9. Classifier , Dust Collector
1. Cement rotary kiln adopts adjustable speed driving with high efficient and low power consumption.
2. The fuel consumption of unit product is low and large capacity.
3. Stable mechanical performance and transmission, accurate speed control and easy control the calcination temperature.
4. Gears: single or double. The rotating speed is controlled by regulating motor, DC motor or variable frequency and speed regulation motor. Be reliable, energy-saving and efficient.
5. Support device: advanced shaft structure, automatic temperature measuring device and electrical heating device.
Technical Parameters of Rotary Kiln
Product specifications(m) | Kiln dimensions | Capacity(t/d) | Rotation speed(r/min) | Motor power(kw) | Total weight(t) | Note | ||
Diameter(m) | Length(m) | Obliquity(%) | ||||||
Φ2.5×40 | 2.5 | 40 | 3.5 | 180 | 0.44-2.44 | 55 | 149.61 | Kiln with shaft cyclone preheater |
Φ2.5×50 | 2.5 | 50 | 3 | 200 | 0.62-1.86 | 55 | 187.37 | ---- |
Φ2.5×54 | 2.5 | 54 | 3.5 | 204 | 0.48-1.45 | 55 | 196.29 | ---- |
Φ2.7×42 | 2.7 | 42 | 3.5 | 320 | 0.10-1.52 | 55 | 198.5 | ---- |
Φ2.8×44 | 2.8 | 44 | 3.5 | 400 | 0.437-2.18 | 55 | 201.58 | Outside disassemble kiln |
Φ3.0×45 | 3 | 45 | 3.5 | 500 | 0.5-2.47 | 75 | 210.94 | ---- |
Φ3.0×48 | 3 | 48 | 3.5 | 700 | 0.6-3.48 | 100 | 237 | Outside disassemble kiln |
Φ3.0×60 | 3 | 60 | 3.5 | 300 | 0.3-2 | 100 | 310 | Alumyte-alumina forge kiln |
Φ3.2×50 | 3.2 | 50 | 4 | 1000 | 0.6-3 | 125 | 278 | Outside disassemble kiln |
Φ3.3×52 | 3.3 | 52 | 3.5 | 1300 | 0.266-2.66 | 125 | 283 | Kiln with preheater precalcine |
Φ3.5×54 | 3.5 | 54 | 3.5 | 1500 | 0.55-3.4 | 220 | 363 | Kiln with preheater precalcine |
Φ3.6×70 | 3.6 | 70 | 3.5 | 1800 | 0.25-1.25 | 125 | 419 | Generating kiln for using ofterheat |
Φ4.0×56 | 4 | 56 | 4 | 2300 | 0.41-4.07 | 315 | 456 | Kiln with preheater precalcine |
Φ4.0×60 | 4 | 60 | 3.5 | 2500 | 0.396-3.96 | 315 | 510 | Kiln with preheater precalcine |
Φ4.2×60 | 4.2 | 60 | 4 | 2750 | 0.4-3.98 | 375 | 633 | Kiln with preheater precalcine |
Φ4.3×60 | 4.3 | 60 | 3.5 | 3200 | 0.396-3.96 | 375 | 583 | Kiln with preheater precalcine
|